Carbon Capture Strategies
- Immanuelraj Soosaiprakasam
- Feb 11, 2023
- 4 min read
There are several different strategies for capturing carbon dioxide (CO2) from power plants and other industrial sources. The most widely used methods include:
Post-combustion capture
In this method CO2 is captured after the point of release (power plants, industrial complexes). Coal or Natural gas when burned in air produces the flue gas that contain CO2 (~5-15% by volume) nitric (200-3000 ppm) and sulfur oxides. A typical coal fired power plant flue gas contain 7 to 14% CO2 and natural gas fired power plant flue gas contains 4% CO2. Combustion is the normal process used in industries to generate the energy they need for their operations and cannot be avoided. The low-pressure flue gas with low concentrations of CO2 is processed using a variety of techniques such as amine-based solvents, chilled ammonia, or membrane separation to separate CO2. Although it is a very matured technology, due to low CO2 capture efficiencies, this strategy is very energy intensive.
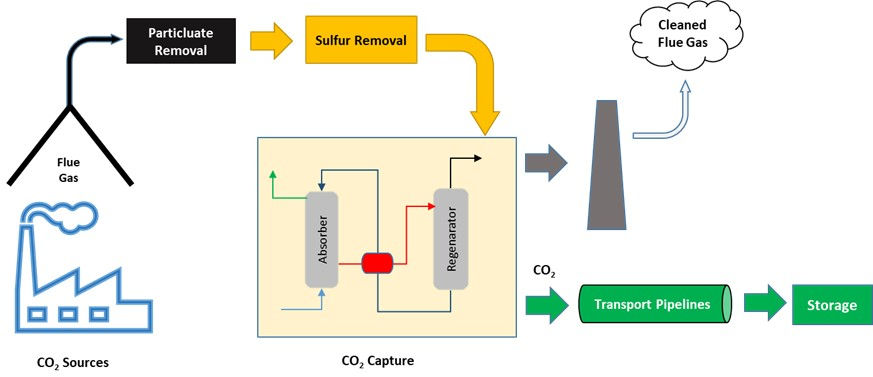
Figure 1 – Post Combustion Strategy
Pros:
Good for existing power plants. It is easy to retrofit with carbon capture unit.
Cons:
The combustion of fossil fuels emits flue gases, which contain sulfur dioxide, nitrogen, water vapor, carbon dioxide, and nitrogen, which cannot be eliminated.
High energy penalty of separating and pressurizing CO2
Implementing carbon capture unit will reduce the overall plant (pulverized coal plant) efficiency by 10-11% points.
Pre-combustion capture
In Pre-combustion method CO2 is captured before the point of release (i.e. before the combustion of fossil fuels is completed).In this process the fossil fuel is converted to a form that releases CO2 when it is burned. For an example, coal can be converted into a synthetic gas (syngas) that is rich in Hydrogen (H2, 25%-30%) and Carbon Monoxide (CO, 30-60%) and Carbon Dioxide (CO2, 5-15%). The syngas is made to react with steam in a process known as water gas shift reaction where the water is broken down into hydrogen and oxygen, the later reacting with some of the CO in the syngas stream to produce CO2. In this process the significant conversion of fossil fuel to hydrogen and CO2 is achieved. The main reactions involved are shown below:
Coal gasification reaction Coal --> CO +H2
Methane reforming reaction CH4 + H2O ---> CO + H2
Water – gas shift reaction CO + H2O ---> CO2 + H2
Water gas shift reaction is exothermic, and the heat is recovered by heat recovery steam generator (HRSG). Once the CO is converted to CO2 and H2, CO2 is separated and H2 is sent to turbine as a fuel for power generation. The heat from flue gas is recovered by HRSG and produce steam. The steam is further used for power generation in a steam turbine.
In this strategy majority of the carbon is converted to CO2 to produce a flue gas stream rich in CO2 (~15-50% by volume) and high in pressure to improve the capture efficiencies. Typical cost of CO2 capture by the plants installed with Integrated Coal Gasification Combined Cycle (IGCC) is around $60/ton of CO2.

Figure 2 – Pre Combustion Strategy
Pros:
Highly efficient and easier removal of CO2.
Minimizes the NOx and SOx emissions.
Low energy penalty of separating and pressurizing CO2
Hydrogen produced from this process could also be used in fuel cells and other clean energy technologies.
Cons:
The gasification process is very expensive compared to traditional pulverized coal power plants.
Retrofitting existing coal plants with IGCC will be expensive and require extensive modifications.
Implementing IGCC will reduce overall plant efficiency (pulverized coal plant) by 7-8% points.
As the flue gas stream is rich in CO2 and at high pressures, physical absorption, pressure swing absorption and membrane capture processes are suitable for this strategy.
Oxy-fuel combustion capture
In traditional combustion process fossil fuel is burned with air. Air contains 21% of O2 and 78% of N2 which produces a flue gas that contain low concentrations of CO2 (5-15%) and rich in nitrogen oxides (NOx) and sulfur oxides (SOx). Oxy-fuel combustion method involves burning the fuel in the presence of oxygen instead of air, which results in a flue gas that is mostly composed of CO2 (80-85%) and steam. The steam can be converted to water by cooling the stream and CO2 can be easily separated. In oxy fuel combustion nearly all the carbon is converted to CO2. Impurtities such as sulfur and nitrogen oxides need to be removed before compressing CO2 for further transportation. These additional steps will make the process ~90% efficient.

Figure 3 - Oxy-fuel Combustion Strategy
Pros:
· Minimizes the NOx and SOx emissions.
· Energy loss associated with separating CO2 from NOx is reduced.
Cons:
· The main disadvantage of this method is the high operational cost for producing O2 and pressurizing CO2 after combustion.
Direct Air Capture
This method involves capturing CO2 directly from the air (~415 ppm of CO2), using adsorbents, chemical reactions, and other processes. In DAC, the atmospheric air is drawn using fans and allowed to pass on to a filter made of solid sorbent that binds the CO2 and remaining air is released to the atmosphere. When the filter is heated up, it will release the CO2 which can be stored in for further use. Some solid adsorbents adsorb CO2 from the air and releases the CO2 when the pressure is reduced (vacuum).
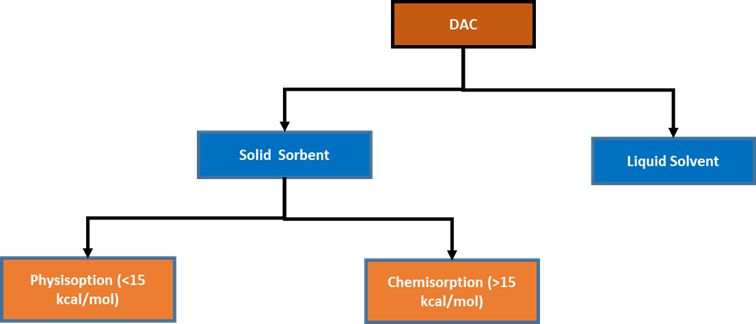
In liquid solvent approach the gaseous CO2 is absorbed into a liquid solvent which is a strong basic hydroxide. This is followed by anionic exchange that precipitates calcium carbonate pellets. Pure gaseous CO2 is recovered from calcium carbonate pellets by applying high temperatures.
Pros:
As DAC captures CO2 from air, it can be deployed anywhere we have accessibility to power and end users/geological storage sites.
No need to build extensive network of pipelines to transport CO2 to storage sites.
Without the need for pipelines the risk of captured CO2 leak to atmosphere is reduced.
Requires smaller land footprint.
DAC systems have the potential to be classified as net carbon negative provided the captured CO2 is sequestered underground or used to make products such as cement or plastics that can trap CO2 for long time while reducing atmospheric concentration of CO2.
Cons:
CO2 concentrations in air is more diluted than industrial emitters making this process expensive due to high energy needs. Most recent estimates show that the CO2 capture cost by DAC could be in the range of $94 to $234/ton of CO2.
Each of these methods has its own advantages and disadvantages. Factors such as the type of power plant or industrial source, the specific emissions profile, and the availability of technology options will determine which method is most appropriate for a given situation.
Comments